Revolutionising Zipper Repair: A Modular and Semi-Automated Solution for Sustainable Fashion
The textile industry is dealing with a major waste issue, both in terms of production infrastructure and consumption culture. Despite some efforts by key players to promote sustainable fashion by encouraging customers to extend the lifespan of their clothing, there is no standardised infrastructure or systematic approach for repairing textile products at scale and a reasonable cost.
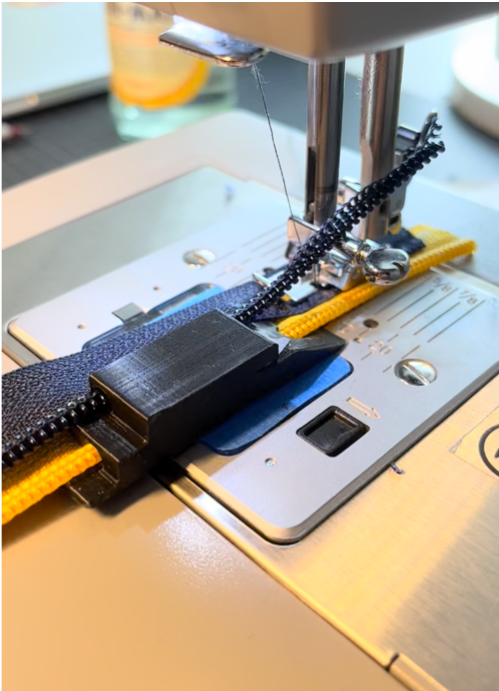
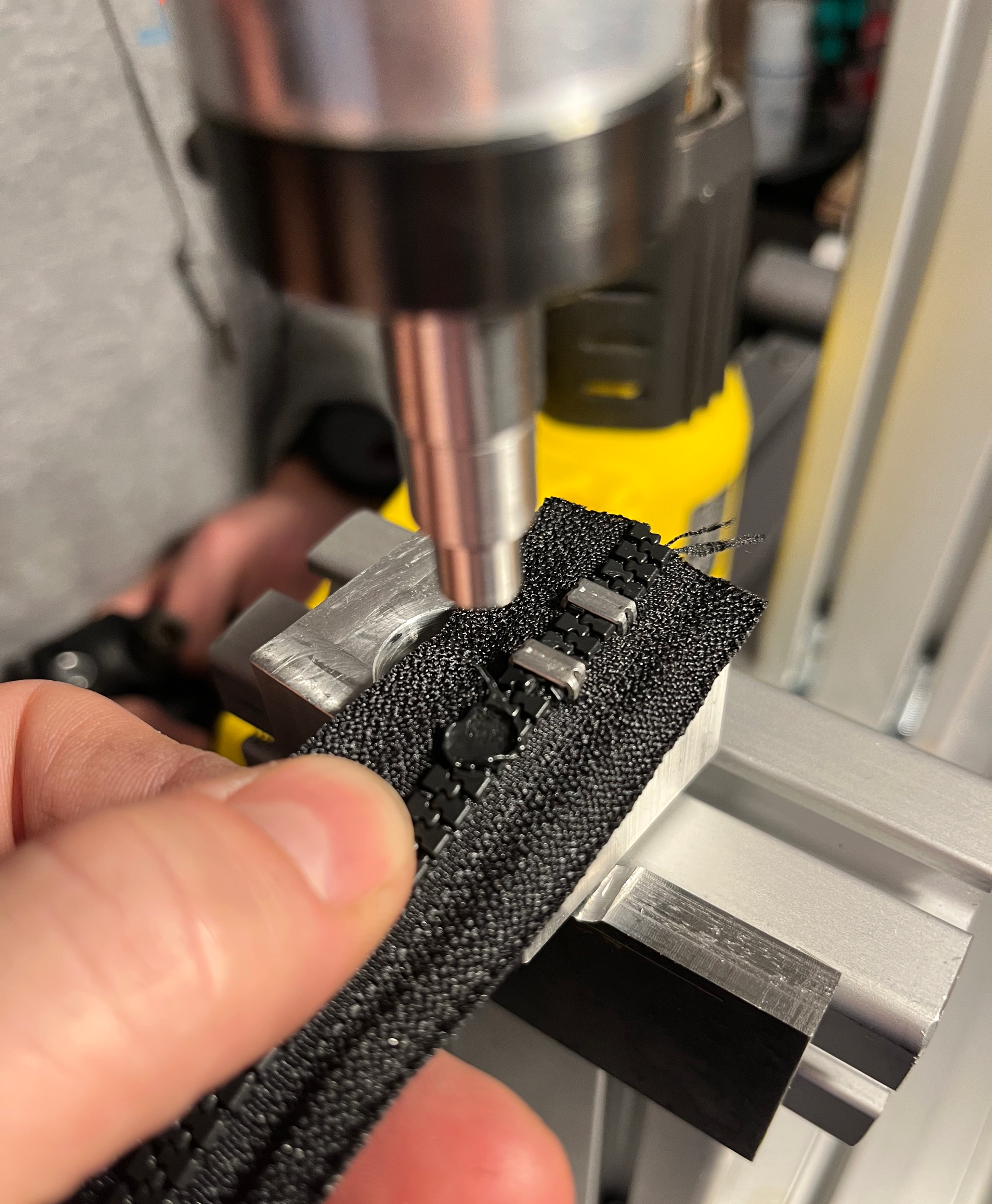
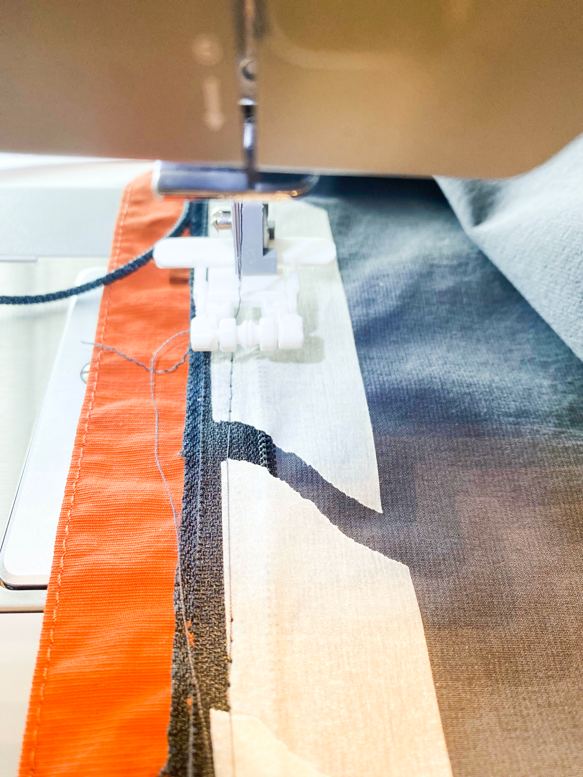
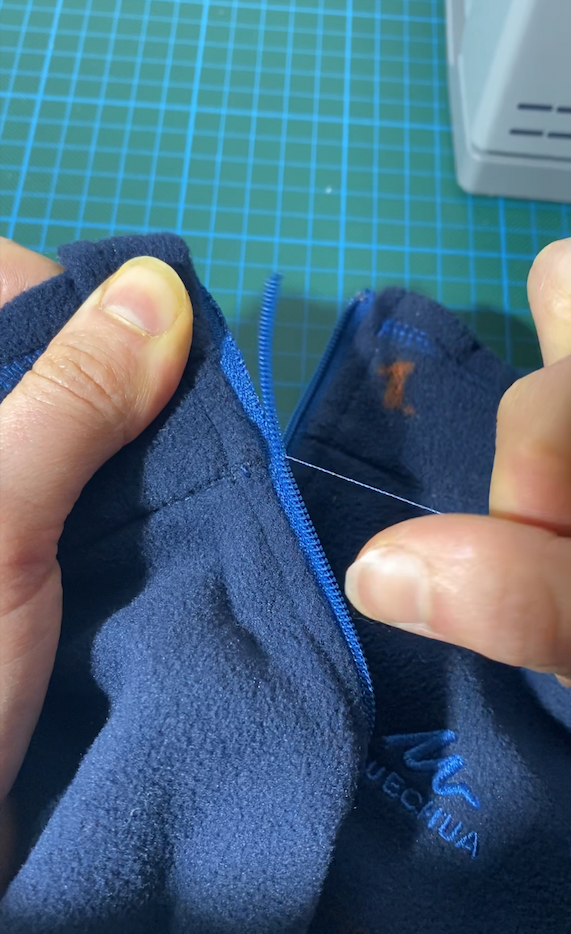
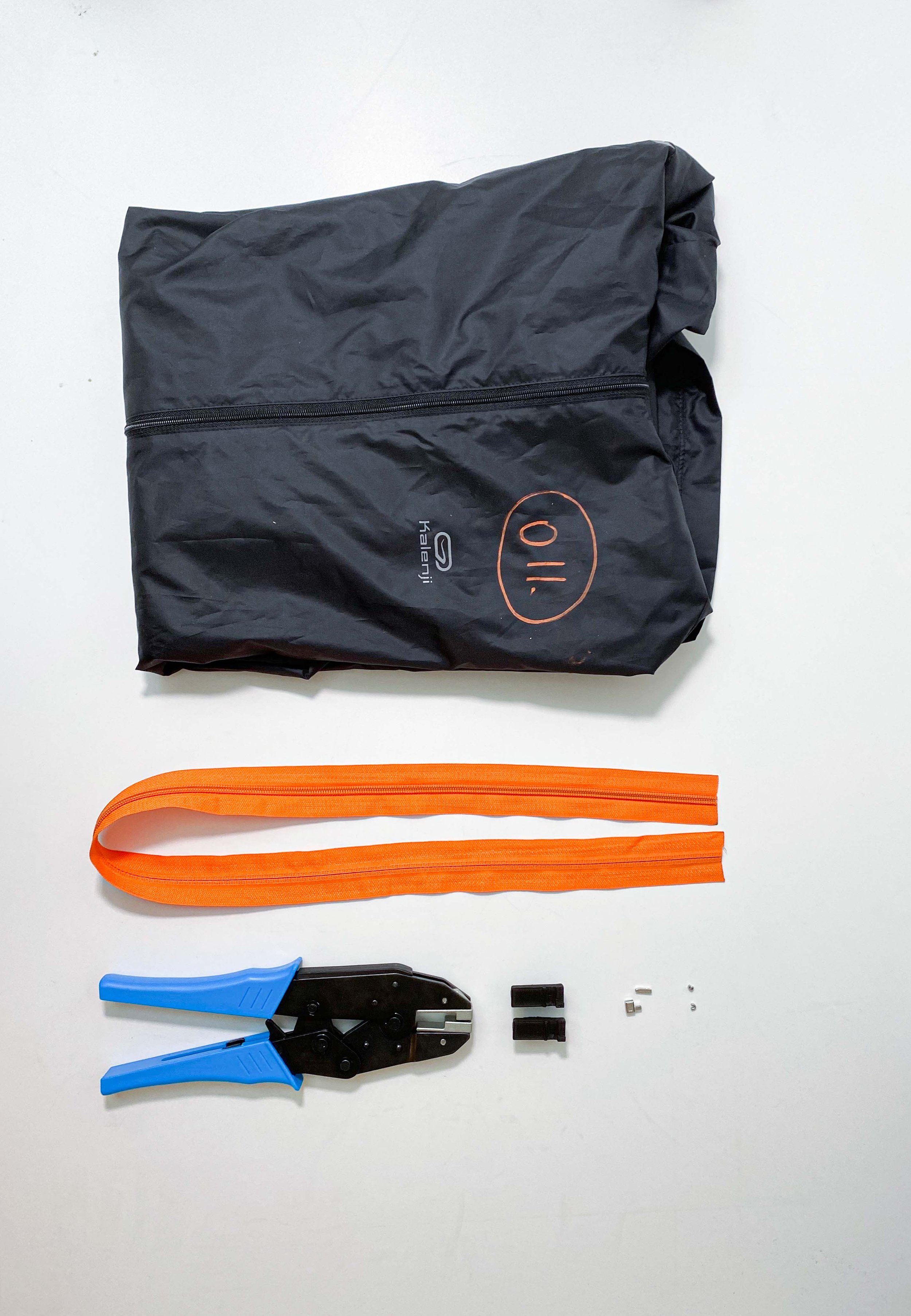
In the first three months of the CISUTAC project, PCH Innovations conducted a context analysis with Decathlon Italy to identify the most relevant repairs to consider. After prioritising repairs based on various factors (occurrence, customer relevance and repair complexity), zipper repair was chosen as the most valuable intervention.
While most zipper repairs are done using standard sewing machines, the process can be challenging and time-consuming (over 40 minutes per zipper) due to the need for specific spare parts and customisation based on the unique size and components of each zipper. To address this issue, PCH Innovations created a modular, semi-automated concept that can adapt to different processes and materials, allowing operators to work more efficiently.
The station includes several modules that enable operators to perform various tasks, such as garment inspection, spare part selection, and repair intervention. The digital interface helps automate the inspection process and identify the type of zipper needed for repair. Custom tools are also available to optimize the removal of old components or the sewing of new zippers, equipped with an automated guiding system for greater precision. To ensure maximum comfort and efficiency for operators, the station also features ergonomic handling structures that keep the garment in the correct position during repairs.
Detailed Repair Principe
Smart Identification Concept Sketch
PCH Innovations is still doing some manual experimentation and tooling exploration to select the best mechanisms for cutting, guiding, and sealing, but has started structuring the entire workflow to cover all possible repair types. They have also started building a digital layer, in collaboration with STAM, to collect data and assist the operator.
While still undergoing manual experimentation and tooling exploration, PCH Innovations plans to pilot the semi-automated station at various locations, including CISUTAC partners De Kringwinkel, Decathlon Italy, and Texaid. The station should take less than 9 days to set up from scratch, and a maximum downtime of 10% of total working time. The objective is to conduct 6 repairs per hour, with less than 10g of waste per repair and a functional check of repair effectiveness.
Looking forward, PCH Innovations is considering designing the station and tooling system to be open sourced, with mountable, interchangeable structure components, printable parts, and replicable deployment. The digital interface will be designed to maximise knowledge transfer among users and stations running in pilots. The immediate next steps consist of engineering critical components, building the digital layer, growing the database, and iteratively developing the station.
Through the CISUTAC project, the hope is to create a more sustainable and efficient approach to textile repair, reducing waste and promoting a more circular economy. PCH Innovations keeps receiving products from Decathlon Italy and De Kringwinkel to validate that this repair workstation works on all relevant products, with the goal of having a first running prototype at PCH Innovations studio by the end of 2023.
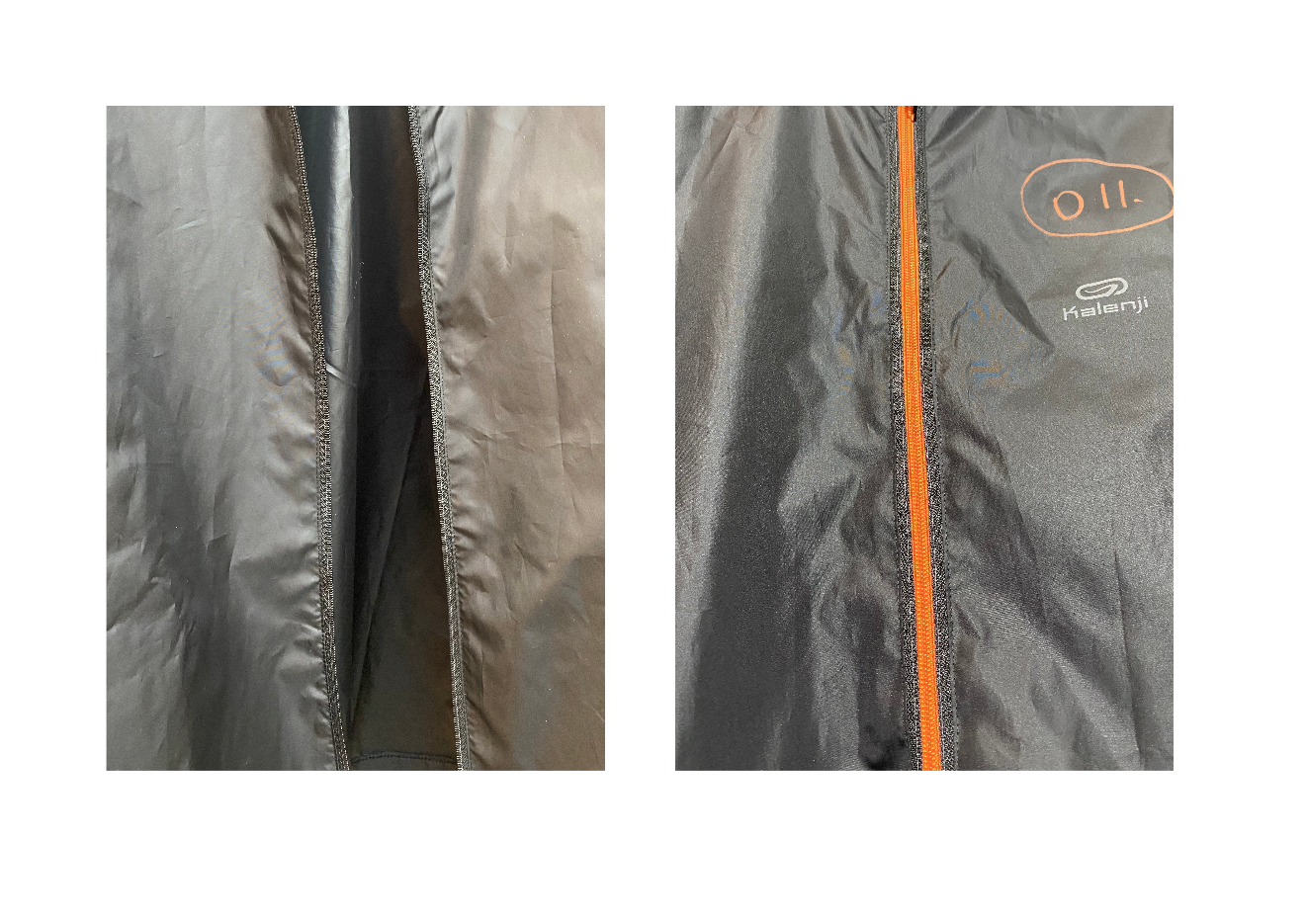
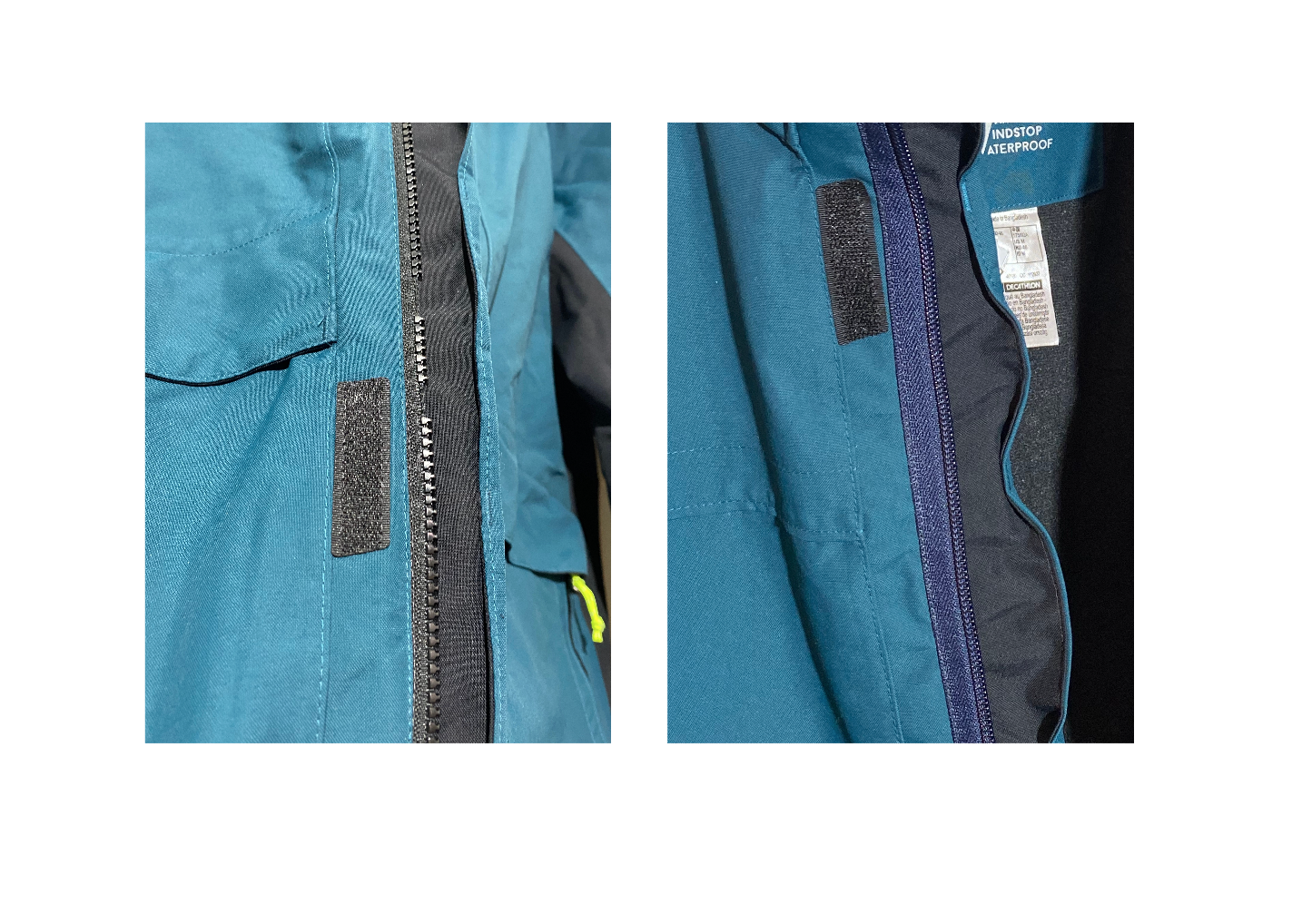
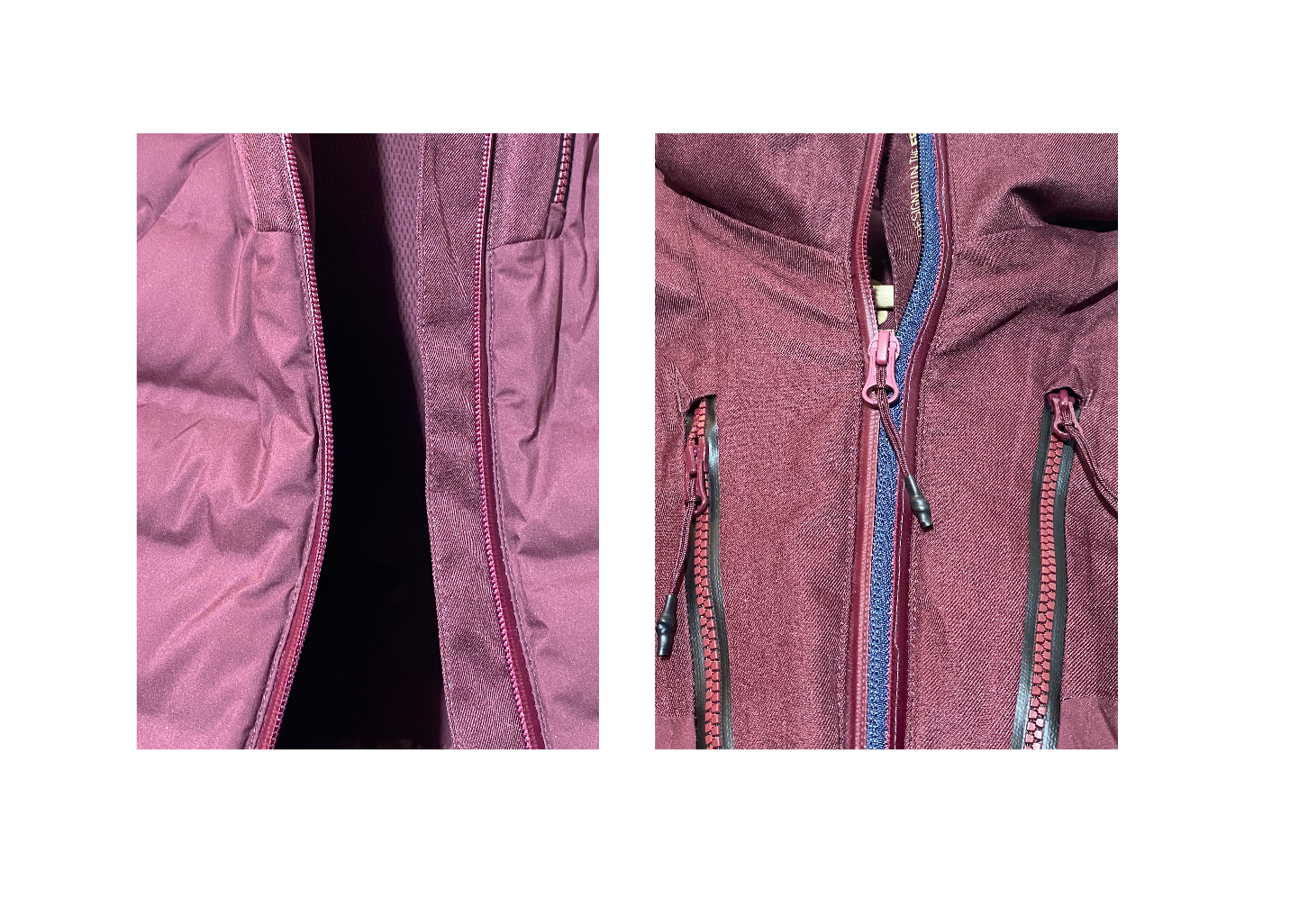
Before-After Sewing Repair