Automatising PPE Recycling: The Future of Firefighter Suit Disassembly
In a world where sustainability is at the forefront of innovation, the recycling of protective workwear presents a unique challenge. Often composed of a diverse mix of materials, including blends and contaminants, personal protective equipment (PPE) such as firefighter suits pose a complex problem in the world of recycling.
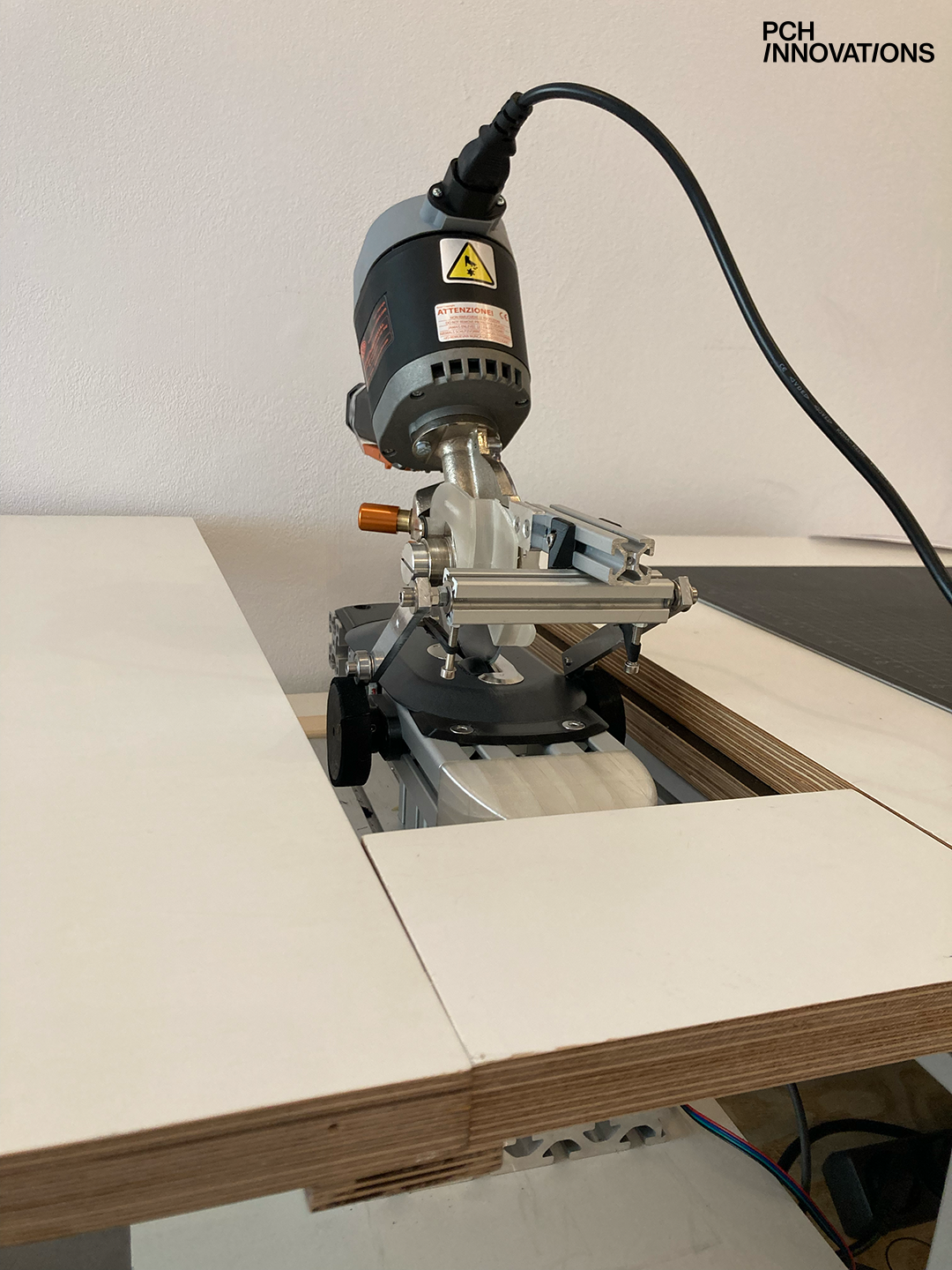
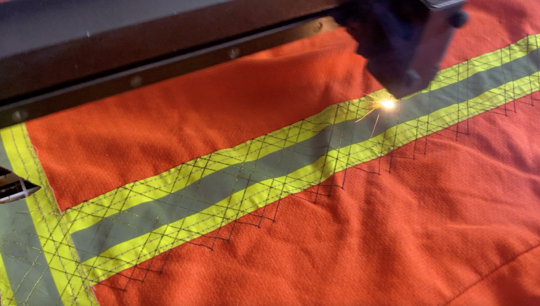
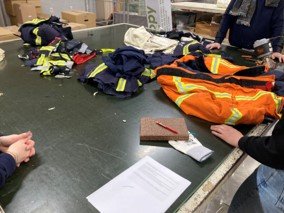
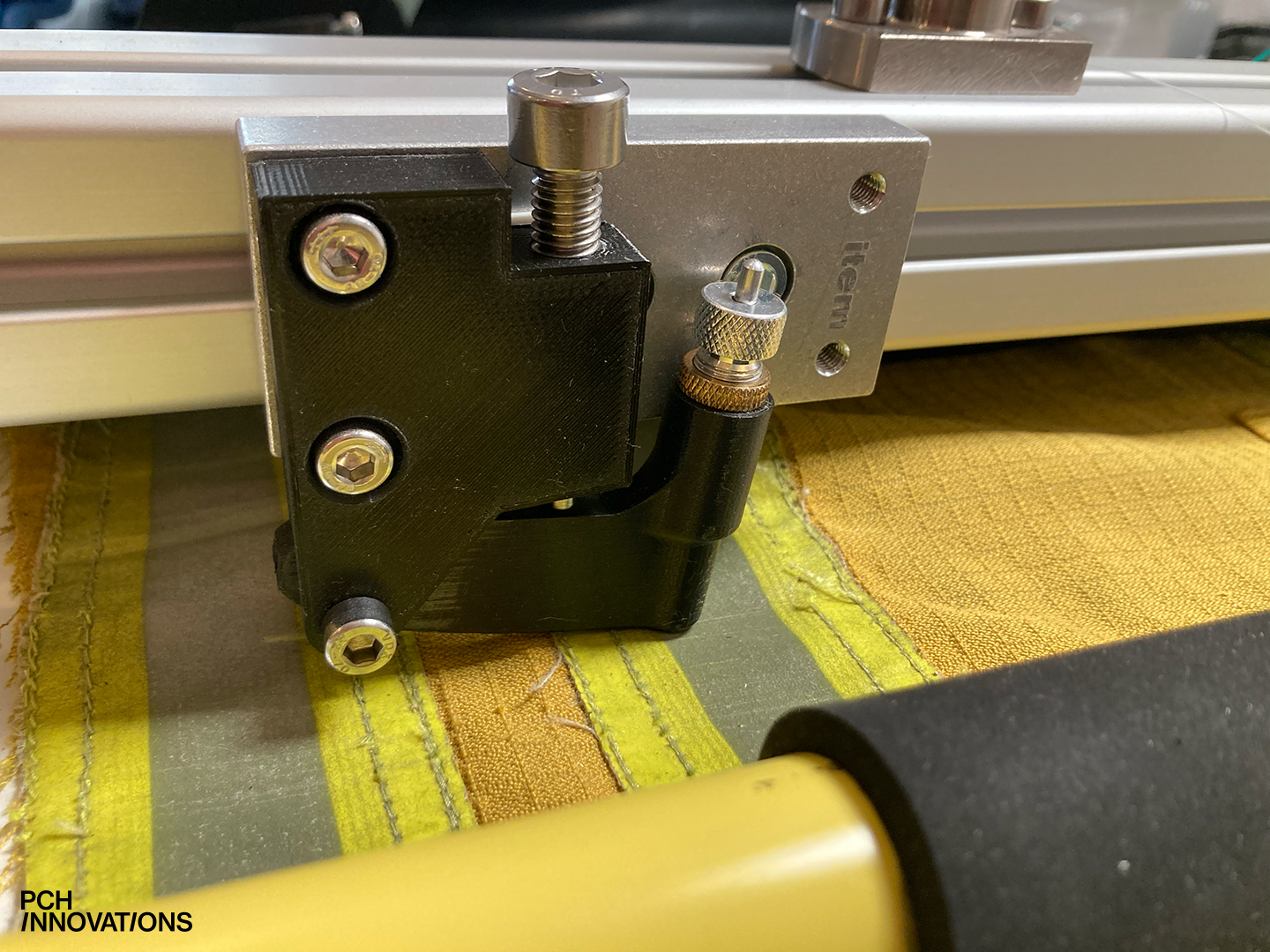
Within CISUTAC, PCH Innovations, SIOEN, STAM and De Kringwinkel are focusing on revolutionising the disassembly of firefighter suits to make recycling more efficient, cost-effective, and sustainable. Today, the disassembly of firefighter suits is a manual, time-consuming, and cumbersome process. Recycling this vital protective gear is not only expensive but also results in recycled fibres that are often more costly than virgin fibres. A significant portion of firefighter suits is made from aramid, a high-performance synthetic fibre. PCH Innovations is on a mission to develop a cutting-edge workstation that maximises the recovery of pure aramid cloth pieces. These pieces can then be processed in mechanical recycling machines to create reusable fibres. CISUTAC’s ambitious goal is to achieve an output of 10 kilograms of aramid per hour, a substantial improvement over current manual methods, which typically represent 300-500% less of this amount.
The challenge in automating this process lies in the vast diversity of firefighter suit compositions and the various applications and components they contain. PCH Innovations quickly realised that removing external applications, particularly high-visibility stripes sewn onto the jackets, was a critical step in streamlining the disassembly process. Using the firefighter suits sent by SIOEN, they explored two concepts for this task: one involved removing the stripes before the garment was cut into pieces, while the other focused on removing them afterward. In the first concept, an adaptive mount for the garment and a robotic arm equipped with a grinder were used to open up all stitches of the high-visibility stripes. The second concept featured a machine capable of opening stitches on flat fabric pieces using a special knife. Both concepts incorporated an electrical scissor for cutting aramid, with an automated feed mechanism and the help of a human worker to place and partially guide the garment during this process.
Overview of the dismantling workstation
The CISUTAC consortium is dedicated to combining the flexibility and adaptability of human workers with smart machines to parallelise work and enhance safety and ergonomics. Clear instructions and well-organised workspaces help expedite the disassembly process. The worker's workflow involves picking up the garment, loading it onto the cutting table, and feeding it through a stationary aramid cutter. Arms, collars, and hems are cut off, and then the layers are separated. Pieces with high-visibility stripes are fed into the application removal machine, which utilises a camera to identify the stripes and a high-speed knife to cut them. The worker can easily remove the stripes once the piece passes through the machine, sorting all cloth pieces into containers beneath the worktable.
The machine being developed by PCH Innovations and STAM is a first of its kind. It promises to greatly improve the current manual disassembly process by enabling the efficient removal of high-visibility stripes and streamlining the entire workflow. The stationary cutter will enhance safety and speed, and the application removal machine will work in parallel, significantly increasing productivity.
The workstation consists of two components: the cutting unit and the application removal unit. Looking forward, these components can be used separately or together, depending on the specific needs of future clients. As the demand for recycling post-consumer textile waste continues to grow, both components will hold value for various stakeholders, including recyclers, collectors, and fashion brands looking to participate in recycling initiatives. They bridge the gap between textile collection and mechanical or chemical recycling processes.
The realisation phase is expected to continue until mid-January 2024, followed by an intensive phase of testing, certification, and documentation through the end of February. Starting in March 2024, the machine will be set up at Kringwinkel Antwerpen to support their staff in the social economy. These designated workstations not only provide Kringwinkel Antwerpen with increased re-use and sorting capacity but also offer invaluable support to their employees. By integrating technology and semi-automation, they facilitate skill development and enhances efficiency without subjecting employees to the pressures commonly found in a regular economic environment. Simultaneously, this period marks the initiation of a pilot phase for the machine, during which, PCH Innovations will collect data and maintain the machine, furthering the goal of creating a more sustainable and efficient approach to recycling protective workwear and promoting a circular economy.